Since this journal post, we have stopped selling personalised cards. We continue to print packaging for our range of vintage lighting products using letterpress and personalise notebooks using mechanical typesetting and letterpress.
Original post: Our Print Club London personalised cards are made by classic letterpress printing and Linotype typesetting. Our adventures in Linotype were covered in an earlier post, so this one is all about plate making and letterpress. Print Club make their posters by screen printing. The technique uses a woven mesh stretched tight in a frame - the screen - which acts like a stencil allowing the transmission of ink in some areas but not others. When ink is applied to the frame using a squeegee it is forced through the open areas to create an image on the paper. The permeable and impermeable areas of the screen are produced photographically or with physical stencils. Screen printing is ideal for large images such as posters. The viscosity and pigment density of the ink create deep tactile colours, and the technique can print onto almost any surface, including uneven and flexible surfaces such as fabric. Traditional screen printing is problematic for greetings cards which are smaller and have larger print runs. The good news is that our letterpress technique produces work of the same quality as screen printing.
When the artwork for the personalised cards arrives from Print Club, it's processed by Rob our studio manager. Rob worked for Hallmark Cards until he jumped ship to Urban Cottage Industries earlier this year. It's proving to be a great move: we are reaping the benefit of Rob's industry expertise, and he gets to exercise the artistic input and creativity which was constrained at Hallmark. Rob works his magic with the images: cleaning, redrawing, scaling and tidying. He then adds the name of the artist, logos, bar code and other card information. When Rob has finished, single colour hi-res files are printed as negatives on matt film using a printer which achieves almost 3,000 dpi. Although the negatives produced are better than photo lab quality, they're still checked carefully by a human eye with the aid of a light box and linen tester.
If the negatives are perfect, the next stage is the creation of print plates from photopolymer sheets. The negative is held against the photopolymer sheet by a vacuum and exposed to light. The light hardens the exposed areas of the polymer. After exposure, the polymer plate is finished by being brushed in nothing stronger than tepid water. The unexposed areas of the polymer swell, get softened by the water and are washed away to leave a plate with a positive image ready for printing. The process is environmentally friendly and creates images as crisp and fine as those produced from metal plates created by acid etching. The whole polymer process is done in-house, which means we exercise complete control over quality and delivery.
If Gutenberg saw one of our Heidelberg machines in action today, he’d be amazed at the level of mechanisation and speed, but the basic process would be instantly recognisable: a stationary bed, moveable platen, inking of the forme, insertion of print material and the closing of the press. The basic principles are unchanged in 500 years, save that wood gave way to metal; first steam and then electrical power was used to open and close the press; a system of rollers was perfected to ink the forme rather than it being done by hand; and mechanical alternatives to hand feeding - manually pushing the paper in and pulling it out - were engineered.
Heidelberg introduced its first platen letterpress machine in 1914. It followed with a mechanically fed press in 1917 and by 1924 it was producing 100 presses per month. Its 15,000th press was delivered in 1932 and by 1959 Heidelberg had delivered 100,000 presses. All our four Heidelberg machines date from the 1950s and early 1960s, so most of our print team are working with machines that were running before they were born.
To print our greeting cards we load up a Heidelberg with a stack of card. The press uses air to separate the sheets - a combination of blowing against the stack and a suction cup to lift the top piece of card. A single piece of card is grabbed by a rotating arm and inserted into the open press where two gauges make sure the card is positioned correctly. The raised image on the forme has already been inked twice by rollers to ensure a complete and even inking. The press then closes automatically and to the right pressure by an ingenious system of pistons, cranks and pivots. The closing of the press prints the card and as the press opens the printed card is grabbed by a rotating arm which takes the card from the press to be stacked. The cards go through the press once for each colour and then a final time for a crease line to be created.
Watching a Heidelberg in action is mesmerising: while one end of the rotating arm pulls a piece of card from the press, the other end grabs a fresh piece of card to insert. It is this mechanism that gives Heidelbergs their American nickname of ‘windmills’ - the rotating arms are like the sails of a windmill. The hypnotic effect is complemented by fleeting glimpses of the inside of the press as it opens, the flash of the inking rollers and the rhythmic clicking, clacking, thumping, blowing and sucking.
Letterpress produces work of a fundamentally different quality to digital print. Our cards have a tactile quality rather than being flat; edges are crisper and more defined; and there is greater depth and contrast in colours. Letterpress also allows us to work with thick cotton-based card stock that has beauty in its irregular texture and fibres. The overall effect is to give our personalised cards an organic quality: the artwork is located in the card rather than sitting superficially on the surface. It's a world away from the industrial photocopiers used by most card companies.
The final quality of our letterpress personalised cards is one that - in a neat piece of synchronicity - they share with the screen printed originals: the impression made by the press is different each time and every card has its own unique qualities. Modern print sometimes fakes these appealing imperfections by using an image which has been digitally manipulated to mimic letterpress. This technique does not create unique print products, merely products which are all identically imperfect.
We are not the first people to be inspired to create new print products using what most consider to be obsolete technology. William Morris founded the Kelmscott Press in 1891 to produce books in the same way and to the same quality as they were produced before the then recent advances in printing technology. We make no claim to have Morris’ artistry or creative drive, but share his view that every aspect of design - images, text, paper and ink - are important and must create a coherent whole. We’ve no problem with functional print, but we firmly believe there's a place for beautiful letterpress.


Original post: Our Print Club London personalised cards are made by classic letterpress printing and Linotype typesetting. Our adventures in Linotype were covered in an earlier post, so this one is all about plate making and letterpress. Print Club make their posters by screen printing. The technique uses a woven mesh stretched tight in a frame - the screen - which acts like a stencil allowing the transmission of ink in some areas but not others. When ink is applied to the frame using a squeegee it is forced through the open areas to create an image on the paper. The permeable and impermeable areas of the screen are produced photographically or with physical stencils. Screen printing is ideal for large images such as posters. The viscosity and pigment density of the ink create deep tactile colours, and the technique can print onto almost any surface, including uneven and flexible surfaces such as fabric. Traditional screen printing is problematic for greetings cards which are smaller and have larger print runs. The good news is that our letterpress technique produces work of the same quality as screen printing.
Plate making for personalised cards


Printing personalised cards
The polymer plates are mounted on a perfectly flat aluminium plate to ensure faultless printing. The plate itself is then mounted on one of our four original Heidelberg platen presses. The origin of platen or letterpress printing are a matter of historical debate. Papers relating to a legal dispute between Joannes Gutenberg (the inventor of movable type in the 15th century) and his financial backer confirm letterpress printing was already in use by the late 1400s. The best explanation is that the printing press originated as an adaptation of similar apparatus used to crush grapes. The printing presses in use in Gutenberg's day consisted of a flat lower surface - the bed - and a moveable upper plate - the platen - which was raised and lowered by means of a screw. The moveable type was locked into a frame - the forme - and placed on the bed. The forme was inked and a sheet of paper pressed against it by the platen which was lowered by the screw.

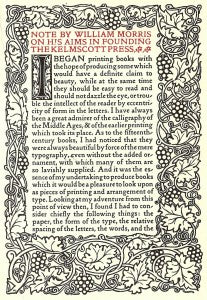



Leave a comment
This site is protected by hCaptcha and the hCaptcha Privacy Policy and Terms of Service apply.